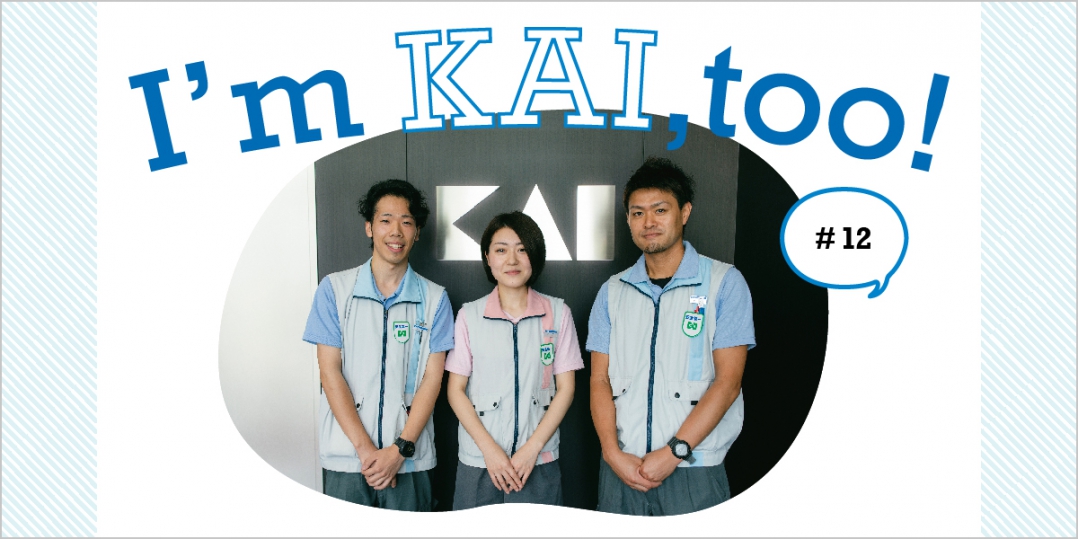
Oyana’s new first factory opened in May 2018. Currently, it serves as KAI’s only razor blade manufacturing factory. It was created in response to growing demand worldwide, mainly in southeast Asia. The factory is producing 80 million blades per month.
“First, we press the razor’s steel to make a hole. Then, after heating it in a furnace at about 1,100 degrees, we’ll quickly cool the steel down. This will make the steel harder. When reheating further, it will become very durable. Next, we will grind the steel with a coarse, fine grindstone to make a sharp cutting edge. This is called the “Three Steps of Sharpening”. This process benefits from many years of KAI experience,” said Sato.
Sayaka Matsui is inspecting blades, visually checking for defects and bad finishes on the cutting edge. “We check 70,000 sheets per hour,” Matsui said. “I have rather good eyesight.” Her attitude showed a great sense of professionalism, which is what KAI is known for.
Ryosuke Ito is responsible for hardening the blades after the inspection. He uses KAI’s “Plasma Ion New process by KAI (PINK)” to coat a titanium alloy and fluororesin. “In this final step, the razor’s shaving ability and durability are greatly enhanced,” Ito said. “The completed blades are sent to other KAI locations, including Shanghai, Vietnam and the Senbiki assembly factory.” They tell us that they want to develop human resource training and new ways to share knowledge. We feel a young energy leading KAI’s future.
①9 years ②When I see products that I’m involved with at a mass retailers ③Learning new skills to gain more work experience ④Shopping and discovering new bars ⑤Tsubasa Honda
①7 years ②When I take one step closer to my goal ③Working toward the next step ④Restaurant hopping ⑤Teppei Koike
①11 years ②When I can solve irregular problems with my own skills ③I want to become a reliable person ④Forget work and play with my children ⑤Mandy Sekiguchi
Questions