PROCESSRAZOR
Press
Stainless steel material for razors is processed by pressing machine. The stainless steel material contains chrome, that makes it difficult to rust, and a few % of carbon, that hardens the blade. The thickness of the material is about 0.1mm. This tape-like material is unrolled and after cutting holes with the pressing machine, it is rolled up again. More than 500 pieces of razor blades are stamped out per minute.
Thermal process
After the pressing process, the stainless steel can still be bent. So, it is hardened by heating it in an electric furnace at 1,000℃ and then rapidly cooling it. By cooling it again at about -80℃, the stainless steel becomes harder. By heating it again, the elasticity of the stainless steel increases and the material becomes hard to break, while maintaining its initial appearance.
Blade edging
The process of forming blade edges by grinding the edge face of hardened stainless steel material with whetstone is called "blade edging". This blade edging process consists in first grinding the material with a coarse whetstone, then grinding it at a more acute angle with a medium whetstone and finally grinding the tip of the blade using a finer whetstone. This technique of sharping thin flat material at acute angle contains the know-how that KAI's factories have accumulated over the years.
Polishing
After the 3rd step of the blade edging process, burrs (ragged edges formed during grinding) can be seen on the grinded blade tips. These burrs are polished using special strops made of cattle hide. By varying the types of strops and the ways to apply them to the blade tips, it is possible to create, with submicron accuracy, blade tips with perfect shapes for shaving and to obtain the finest sharpness.
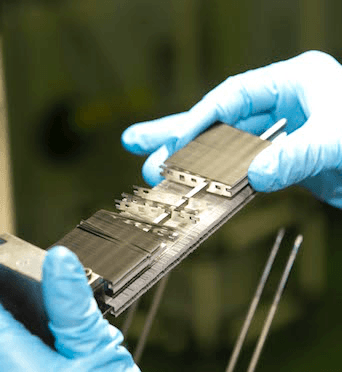
The secret that allows the total inspection of large quantity of razor blades
Looking at the skewered bunch of razor blades, you can notice that they curiously seem to be painted black with ink. This because the blade edges are sharpened to 0.01μm, and they do not have spaces that can reflect light. Therefore we can say that a blade reflecting light has an angle which is not appropriate. So, razor blades are visually inspected lighting them with fluorescent lamps.
Inspection (blades)
Polished razor blades are separated into single pieces at this stage for the first time, then, they are bunched together and skewered. The back of the blade has the typical luster of stainless steel, but on the contrary, the sharp blade tip does not reflect the light and appears to be black. If the blade tips reflect light, it means that they do not have enough sharp angle and that they are defective products. Each razor blade is visually inspected in this way.
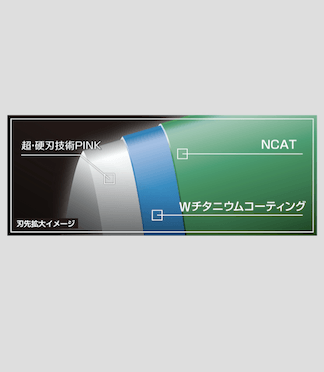
"PINK", KAI's unique technology of improving maximally the blades' durability
"PINK", one of KAI's unique latest technologies that was developed in 2008, increases the hardness of the blade edge by 70% compared to conventional products. By strengthening stainless steel with PINK processing before the coating process, it is possible to reduce to a minimum the cut resistance and to avoid nicks in the blade during use.
Coating / burning
Maximally sharpened blades are coated with hard metal film in order to make them difficult to be worn away. This coating has also the purpose to make blade tips difficult to rust. Blades are additionally coated with fluorine resin, in order to allow them to move smoothly across the skin. Then, resin is heated and melted to form a film on the surfaces. This two layer coating greatly improves the sharpness and the durability of razors.
Plastic molding
The plastic handles of the razors are produced by pouring heated and melted resin into molds. Two-color handles are produced by pouring and molding together two different color resins. The handles of "Besty" are made of soft rubbery resin, that gives them a good grip feeling. This technology was introduced during the development of the product, in collaboration with the Research Institute of Human Engineering for Quality Life.
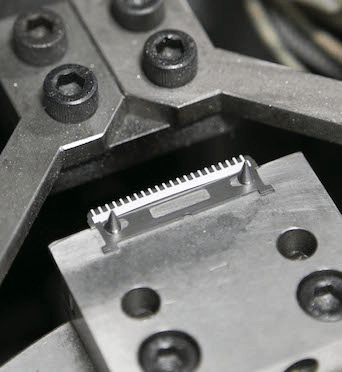
In-house developed razors assembly processing machine
KAI factories' razor assembling machines are almost entirely designed and produced in-house. This allows not only to make improvements in accordance with the evolution of razors and to flexibly meet the need of producing new lines of products, but also to reflect quickly and finely the requests and the evaluations from the field.
Assembling (head)
A 0.05 thick aluminum plate is inserted between the upper and the lower blade, resin parts, called "top" and "bottom", are placed on the upper and lower blade and the razor's head is completed. Last of all, water-soluble resin, that allows the razor to move smoothly across skin during shaving, is applied and the razor's head is definitively completed.
Assembling (handle)
The razor assembling machine was manufactured in-house. The handles are aligned in the same direction utilizing vibration by a device called "Parts feeder". Then, completed razor heads reach the handles, and razors are assembled one by one at high speed.
Inspection / Packaging
Once the razor heads and the handles are assembled together, completed razors are aligned on the conveyor by a robot and then they are put in bags. At this stage, various sensors, put on the assembling machine and on the conveyor, check abnormalities, position of the resin parts, assembly precision and many other check items. In this way, high quality razors are completed.