PROCESSNAIL CLIPPERS
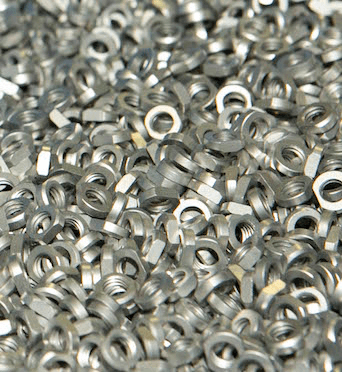
The "Self manufacture" supporting KAI's product manufacturing
In order to guarantee high quality production, KAI continuously makes efforts to complete in-house as many processes as possible, developing and designing small parts such as screws for nail clippers and scissors, and various processing machines, such as the machine for the molding of plastic components and the packaging machine.
Press
The coil-like stainless steel is unrolled, and fed to the pressing machine. In the molds, six or seven processes, such as cutting holes, impressing the mark, bending the blade edges, are continuously carried out. The parts of upper and lower blades which will be the blades of nail clippers are completed.
Welding
The upper and lower blades completed in press process are welded in the form of each blade facing. The welding method is to flow electricity from electrodes when pressing the joint surface hard. The surface of stainless steel starts to melt by the produced heat, and is welded. This process is called spot welding, and commonly used for installation of car body.
Thermal process
The spot-welded nail clipper is moved to a furnace. Cooling it to water temperature rapidly after heating it at about 1000°C changes its structure, and enhances hardness of the stainless steel. Then when heating it again at high temperature of about 180°C, around the weld is softened by heating with high frequency wave because the part of a handle will be a spring of the nail clipper. This process is called “set the part back”, and important for opening and closing nail clippers smoothly.
Shot blasting
The process for the matte blades to smooth the surface. The blades are hit with the high speed glass beads by force of air.
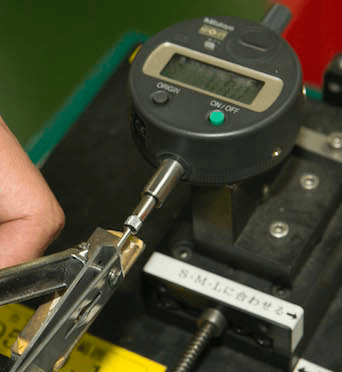
"Lap", the sign of sharp nail clippers
When viewed from the side, you can see that the upper blade in not perfectly in line with the lower blade. This kind of structure is called "lap". Two blades with hard sharp edges may easily be damaged if they bump into each other. For this reason, KAI decided to move the position of the upper blade 0,1mm from the lower blade. This process of displacement of the blade requires great subtlety, because if this distance between the two blades were smaller, the displaced blade edge would try to return at the original position when clipping the nails and would be damaged, if it were larger, the nail clipper would become dull.
Blade edging
The tip part of the nail clipper is sharply edged by pressing it to a finer belt. The nail clipper becomes sharp at this stage for the first time. After edging the blade, it is thoroughly cleaned, dried, and then moved to the next assembly process.
Blade broadening / Structure / Inspection
The engagement of blades characterizes sharpness of nail clippers. When each hard blade edge contacts one another, the blade edges are worn away, and transformed. The position of the upper blade is moved a little from the lower blade to avoid this. The gap is called “lap”. The precise adjustment is required because setting the lap determines sharpness and strength. The blades are broadened, and the covered blades of the nail clipper are attached to the hold-down part called lever, finally, the nail clipper is completed after checking its sharpness by cutting the test paper with it.
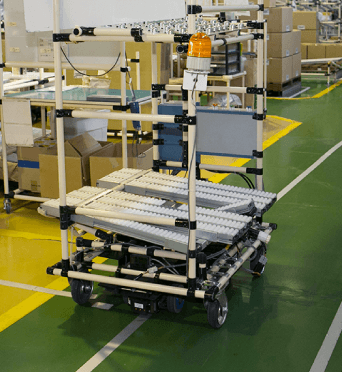
In-house developed Automatic Guided Robot AGV
AGV stands for Automatic Guided Vehicle. It carries automatically parts and materials necessary for the assembly and the packaging from the material yard to a specific place. This transportation robot was developed in-house in order to optimize transportation operations that until then were carried out by workers, and it moves along guide-paths previously set on the floor.
Packaging
The nail clippers that pass the inspection of sharpness are attached to the plastic case preventing the nails from flying off, and then are packed.
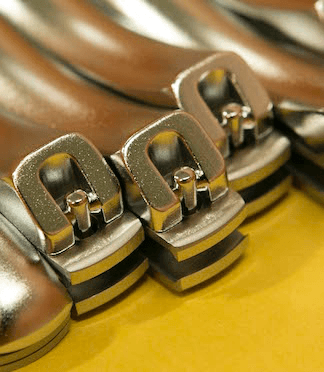
Nail clipper for ingrown nails, satisfying a wide range of customer demands
Nail clippers with normal shaped blades do not fit to ingrown nails and if you try to clip them forcibly from the sides, the nails may crack. The convex blades nail clipper was originally developed in order to solve this problem. The blades were improved and were given a convex shape that fits to ingrown nails, making it possible to clip them easily. In particular, "Square-cut" is a product that allows clipping the center of the ingrown nail with the convex blades and then cutting the nail straight across with the straight blades.